Projektowanie wałów napędowych
Spis treści
Proces projektowania wałów napędowych
-
Funkcja wału napędowego
-
Wyznaczenie minimalnych średnic wału
-
Obrys wstępny wału na zarysie teoretycznym
-
Podstawowe wymiarowanie wałów napędowych
-
Ustalenia szczegółowe
-
Zapewnienie współpracy wału z innymi elementami maszyny
Projektowanie wałów napędowych ze względu na kryterium wytrzymałościowe
Współczynnik redukcyjny dla obciążeń statycznych
Projektowanie wałów napędowych ze względu na kryterium sztywności
Obliczenia sztywności skrętnej wałów.
Konsturkcyjne porady przy projektowaniu wałów napędowych
-
Statyczne wyważanie wału
-
Dynamiczne wyważanie wału
-
Unikanie ostrych karbów
-
Dobrać odpowieni materiał na wały
Proces projektowania wałów napędowych
Aby poprawnie rozpocząć proces projektowania wałów napędowych należy wiedzieć jak wygląda cały przebieg i proces projektowania wału. Poniżej przedstawiliśmy w punktach krok po kroku jak wygląda taki proces projektowania.
1. Funkcja wału napędowego– co jest na nim obsadzone i w którym miejscu.
Pierwszym krokiem w projektowaniu wałów napędowych jest dokładne określenie funkcji wału w maszynie oraz elementów, które będą na nim osadzone. Ważne jest, aby wyznaczyć miejsca, gdzie znajdują się koła zębate, łożyska, lub inne komponenty. Wyznaczenie tych elementów pozwala na wyznaczenie obciążeń oraz na wykonanie dokładnego schematu, który posłuży do dalszych obliczeń uproszczonych (belkowych) i pozwoli określić, w jakich miejscach wał będzie najbardziej zagrożony. Schemat obciążeń jest kluczowy do dalszych etapów projektowania, w tym obliczeń wytrzymałościowych i zmęczeniowych.
2.Wyznaczenie minimalnych średnic wału w miejscach charakterystycznych – Kolejnym etapem jest wyznaczenie minimalnych średnic wału w miejscach, gdzie występują szczególne obciążenia, takie jak czopy, osadzenia łożysk czy koła zębate.
W tym etapie określamy, jakie średnice są wymagane, aby spełniały kryteria wytrzymałościowe, sztywnościowe lub zmęczeniowe. To pozwala na dobór odpowiednich wymiarów wału w poszczególnych miejscach, gdzie występują naprężenia. Może to również obejmować obliczenia oparte na dopuszczalnych naprężeniach, które pomogą w określeniu optymalnych średnic.
Wyznaczenie teoretycznego zarysu wału – Teoretyczny zarys wału to najmniejszy dopuszczalny teoretyczna geometria dla wału, który powinien spełniać wymagania zgodne z danym kryterium. Nie uwzględnia taki zarys tolerancji, pasowań, rzeczywistych średnic czopów ani podcięć obróbkowych.
3. Obrys wstępny wału na zarysie teoretycznym – obrysowanie rzeczywistych wyidealizowanych geometrii wału dla danego zarysu teoretycznego.
Na tym etapie dokonujemy szczegółowego obrysowania rzeczywistego kształtu wału w oparciu o teoretyczny zarys. Uwzględnia się wszystkie istotne elementy, takie jak podcięcia, rowki, otwory na łożyska, a także miejsce osadzenia kół zębatych. W tym momencie warto zwrócić uwagę na takie parametry jak grubość ścianek, promienie zaokrągleń i dokładność wykonania. Obrys ten staje się wyjściowym punktem do dalszego szczegółowego wymiarowania.
4. Podstawowe wymiarowanie wałów napędowych- określenie gabarytowej geometrii i najważniejszych średnic.
W tym kroku określamy gabarytową geometrię wału, uwzględniając najważniejsze średnice, takie jak średnice czopów, które będą pełniły rolę osadzenia kół zębatych, łożysk lub innych elementów. Dokonujemy analizy, aby upewnić się, że średnice czopów są wystarczająco duże, by zapewnić odpowiednią wytrzymałość zmęczeniową, co jest szczególnie ważne w przypadku obciążeń cyklicznych.
Zaleca się aby skok sąsiednich średnic spełniał warunek D/d ≤ 1,2 aby zapobiec koncentracji naprężeń przy przejściu średnic.
5. Ustalenia szczegółowe – Ten etap obejmuje bardzo szczegółowe aspekty wykonania wału, które są kluczowe dla jego długotrwałej eksploatacji oraz efektywności pracy w maszynie. Ważne jest ustalenie:
- Dokładności wykonania pasowań – zapewnienie, że pasowania wału i elementów z nim współpracujących będą odpowiednie dla zapewnienia bezpiecznej pracy (np. pasowania łożysk, pasowania czopów pod połączenie).
- Promienie zaokrągleń – odpowiedni dobór promieni zaokrągleń w miejscach przejść między różnymi średnicami zapobiega koncentracji naprężeń i zwiększa wytrzymałość zmęczeniową. Można zastosować podcięcia obróbkowe i technologiczne z PN−58/M−02043. Geometrie dostępne także na naszej stronie z rysunkiem technicznym.
- Znormalizowanie rowków i podcięć na wale – jeśli wał ma rowki pod łożyska, gwinty lub inne elementy, ważne jest, aby były one zaprojektowane zgodnie z normami.
- Chropowatość powierzchni – odpowiednia chropowatość powierzchni wału ma wpływ na jego trwałość, szczególnie w miejscach współpracy z łożyskami czy kołami zębatymi.
- Tolerancje kształtu i położenia – dokładność wykonania poszczególnych elementów wału jest istotna dla poprawnej współpracy z innymi komponentami.
- Obróbka cieplno-chemiczna – zaprojektowanie odpowiednich procesów obróbki cieplno-chemicznej, takich jak hartowanie, nawęglanie, czy azotowanie, ma na celu poprawę twardości powierzchni wału i zwiększenie jego odporności na zużycie oraz zmęczenie.
6. Zapewnienie współpracy wału z innymi elementami maszyny
Wał jest częścią szerszego układu maszynowego, dlatego konieczne jest zapewnienie jego odpowiedniej współpracy z innymi elementami. Należy uwzględnić elementy takie jak sprzęgła, czy inne mechanizmy napędowe współpracujące z wałem.
Projektowanie wałów napędowych ze względu na kryterium wytrzymałościowe
Pierwszą czynnością którą musimy zrobić to sprowadzić wał do konstrukcji belkowej z oznaczonymi siłami i reakcjami na podporach. Z tego wyznaczamy momenty działające na wale oraz rozkłady obciążeń ścinających i skręcających. Zazwyczaj w wałach głównym komponentem naprężeń jest moment skręcający i gnący i to na nich skupimy się w dalszych rozważaniach. Dla wałów dlugich dla których l/d > 5, należy dodać komponent od ścinania.
Moment wypadkowy gnący występuje w dwóch płaszczyznach XY, XZ zaznaczonych na rysunku, przecinających się w osi geometrycznej wału. Poniżej przedstawiono rysunek w aksonometrii przedstawiający momenty gnące oraz moment zastępczy będący sumą wektorową tych momentów.
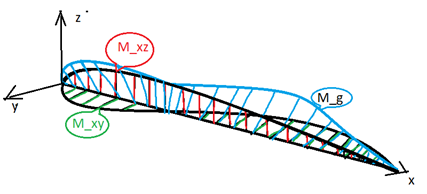
Wzór na moment gnący wypadkowy przyjmuje postać :
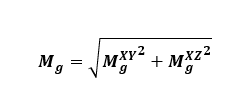
W przypadku obciążeń zmiennych nie można stosować hipotezy wytężeniowej Hubera, z uwagi na to, iż wał się obraca – często z wysoką prędkością – stąd też obciążenie jest zmienne
Wzór przekształcający hipotezę Hublera, uwzględniający zmienne obciążenie wału
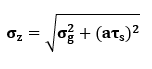
gdzie:
a – współczynnik redukcyjny
Gdzie :
Zg – trwała wytrzymałość zmęczeniowa przy zginaniu
Zgo – z obracającym się wektorem obciążenia
Zgj – z jednostronnym wektorem obciążenia
Zs – trwała wytrzymałość zmęczeniowa przy skręcaniu
Zso – z obracającym się wektorem obciążenia
Zsj – z jednostronnym wektorem obciążenia
Istotny stosunek długości wału do średnicy:
![]() |
Gdy stosunek długości do średnicy wału jest większy niż 5 to nie liczymy τt z uwagi na zbyt mały udział naprężeń stycznych. |
Współczynnik redukcyjny dla obciążeń statycznych:
Dla obciążeń statycznych można przyjąć, że granica plastyczności w przypadku zginia i rozciągania jest 1,73 większa niż granica plastyczności w przypadku skręcania.
dla obciążeń statycznych → | ![]() |
Naprężenia zredukowane dla wałów rozszerzone o współczynnik redukcyjny przyjmują postać
Zasady redukowania momentów występujących na wale do momentu zastępczego :
W przypadku dominacji momentu gnącego Mg należy zastosować poniższe wzory aby zredukować moment do momentu zastępczego. Poniższe równania przedstawiają także wzór na średnicę minimalną wału w ranym przekroju.
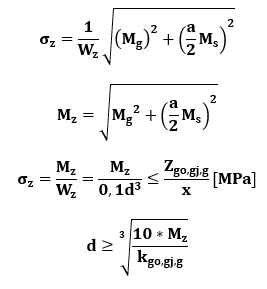
W przypadku dominacji momentu skręcającego Ms wzory redukcyjne przyjmują poniższe formy:
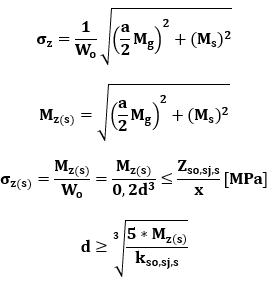
Wały obciążone tylko momentem skręcającym obliczamy z warunku zawartego równaniem:
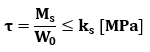
Gdzie:
k_s – naprężenia dopuszczalne dla materiału z którego wykonany jest wał.
W_o – wskaźnik wytrzymałości przekroju na skręcanie
Uzależniając obliczenia od przenoszonej mocy N i prędkości obrotowej wału n.
Poniżej przrdstawiony został wzór na średnicę czopa wału w zależności od przenoszonej mocy i prędkości obrotowej wału.
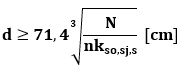
Gdzie:
k_so,sj.s – naprężenia dopuszczalne dla materiału, z którego wykonany jest wał, na skręcanie obustronne, skręcanie jednostronne i ścinanie.
Projektowanie wałów napędowych ze względu na kryterium sztywności
Obliczenia sztywności wałów poprzecznej – giętej
Maszyny w których sztywność wału jest ważniejsza niż wytrzymałość:
- wrzeciona obrabiarek
- przekładnie zębate
- długie wały przenoszące obciążenia na inne elementy –np. pasy i koła zębate
Miarą odkształcenia (sztywności) jest ugięcie y i kąt pochylenia linii ugięcia (przekoszenie) β. Najczęściej interesuje nas maksymalna strzałka ugięcia oraz kat pochylenia linii ugięcia fmax [mm] w miejscu usadowienia podpór, w przypadku wałów – na łożyskach.
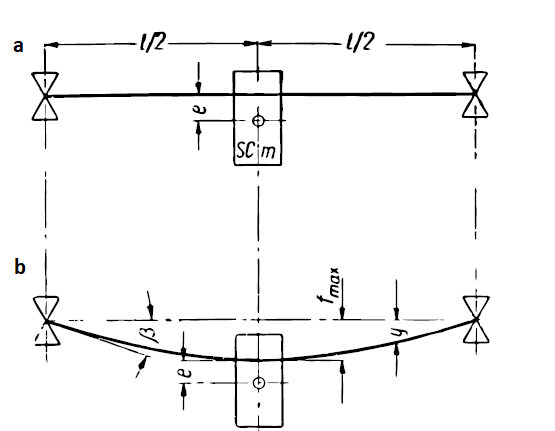
Schemat wału obciążonego niewyważoną masą a – w spoczynku, b – w ruchu
Przybliżone równanie lini ugięcia belki – elementu wyjściowego do obliczania wałów:
Kąt przekoszenia β:
Ugięcie:
Maksymalna strzałka ugięcia nie powinna przekraczać:
dla wałów maszynowych | ![]() |
dla wałów przekładni zębatych | ![]() |
dla silników elektrycznych | ![]() |
Maksymalne przenoszenie:
– w łożyskach ślizgowych:
- sztywnych βdop = 0,3 · 10-³ [rad] = 0,017 [º]
- samonastawnych βdop = 1 · 10-³ [rad] = 0,057 [º]
– w łożyskach samonastawnych:
- βdop = 1 · 10-³ [rad] = 0,057 [º]
– w łożyskach tocznych stożkowych:
- βdop = 1 · 10-³ [rad] = 0,057 [º]
– w łożyskach tocznych walcowych
- typu N i NU βdop = 25 · 10-³ [rad] = 1,432 [º]
- inne postacie: βdop = 0,5 · 10-³ [rad] = 0,029 [º]
Maksymalna strzałka ugięcia jak i kąt przenoszenia może ulegać zmianie w zależności od wymagań stawianych elementom maszyn.
Obliczenia sztywności skrętnej wału napędowego.
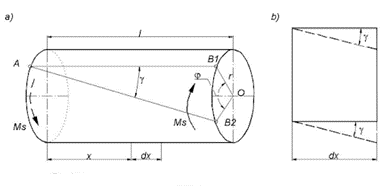
Sztywność skrętna – oceną parametru sztywności skrętnej jest odkształcenie kąta skręcenia φ na odcinku l od zadanego momentu skręcającego
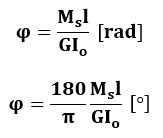
Gdzie:
Ms – moment skręcający [Nm]
G – moduł sprężystości poprzecznej [N/m²]
Io – biegunowy moment bezwładności przekroju [m^4]:
Dla wału kształtowego złożonego z wielu mas ustawionych w szeregu:

Dopuszczalne wartości kąta skręcenia dla wału o długości l = 1m → 0,25º-2,5º
Konstrukcyjne porady przy projektowaniu wałów napędowych
Aby zapewnić wałom jak najlepsze parametry pracy oraz wydłużyć ich trwałość podaliśmy poniżej ogólne porady konstrukcyjne. Te porady zapewnią jak najlepsze użytkowanie, zminimalizują szansę na uszkodzenia wału w trakcie pracy oraz zapewnią lepszą współpracę wału z innymi urządzeniami w maszynie.
Wyważanie wału statyczne i dynamiczne – wyważanie wału w celu usunięcia momentu od pary sił odśrodkowych.
Wyważanie wału to proces, którego celem jest zminimalizowanie lub całkowite usunięcie sił i momentów powstających w wyniku nierównomiernego rozkładu masy. Te siły mogą powodować drgania, hałas, zużycie łożysk oraz inne niepożądane efekty w działaniu wału i całej maszyny.
Statyczne wyważanie wału
Statyczne wyważanie odnosi się do sytuacji, gdy środek masy wału znajduje się poza jego osią obrotu, ale wał jako całość nie ma momentów bezwładności związanych z niesymetrycznym rozkładem masy.
Wał jest montowany na dwóch swobodnie obracających się rolkach. Jeśli wał nie jest wyważony, cięższy punkt powoduje obrót wału do pozycji dolnej. Korekcja wyważenia polega na dodaniu masy w przeciwnym miejscu lub usunięciu nadmiarowej masy, aby środek masy wału znalazł się na osi obrotu.
Wał jest wyważony w stanie spoczynku (statycznie). Wyważanie statyczne jest odpowiednie dla wałów obracających się z niskimi prędkościami, gdzie siły dynamiczne nie mają znaczącego wpływu.
Statyczne wyważanie nie eliminuje momentów wynikających z par sił odśrodkowych, które mogą się pojawiać w ruchu obrotowym przy wyższych prędkościach.
Dynamiczne wyważanie wału
Uuwzględnia nie tylko przesunięcie środka masy wału, ale także momenty generowane przez pary sił odśrodkowych na różnych płaszczyznach wału podczas ruchu obrotowego.
Wał jest montowany w maszynie wyważającej, która może obracać go z określoną prędkością. Czujniki w maszynie wyważającej wykrywają Siły odśrodkowe: Wynikające z nierównomiernego rozmieszczenia masy oraz moment generowany przez pary sił odśrodkowych działające w różnych płaszczyznach.
Proces korekcji wyważania polega na dodaniu masy w odpowiednich miejscach i usunięciu masy w miejscach przeciwnych.
Wyważanie może być przeprowadzane w jednej płaszczyźnie (dla krótkich wałów) lub w dwóch (dla dłuższych i złożonych).
Dynamiczne wyważenie eliminuje zarówno siły odśrodkowe, jak i momenty wywołane przez pary sił. Wał jest stabilny podczas pracy z wysokimi prędkościami obrotowymi, minimalizując drgania i zużycie.
Przykład momentu od pary sił odśrodkowych
Jeśli wał ma nierównomiernie rozłożoną masę, mogą wystąpić sytuacje, gdzie w różnych częściach wału pojawią się niesymetryczne siły odśrodkowe. Siły te działają w przeciwnych kierunkach w różnych punktach wału, tworząc parę sił, która generuje moment odśrodkowy. Moment ten powoduje drgania giętne i obciążenie łożysk. Przy wyższych prędkościach obrotowych może doprowadzić do rezonansu i awarii.
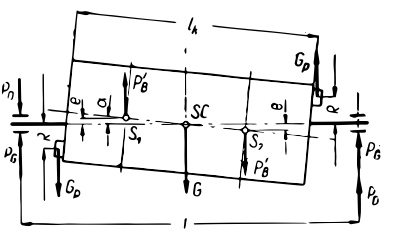
Unikanie ostrych karbów
Ostre karby są miejscami koncentracji naprężeń, mogącymi prowadzić do pękania zmęczeniowego i skrócenia żywotności wału. Unikanie ich w projektowaniu wałów jest kluczowe dla zapewnienia wytrzymałości, trwałości i niezawodności całego układu mechanicznego.
Czym są karby i dlaczego są niebezpieczne?
Karby to zmiany geometryczne, jak nagłe przejścia między średnicami, rowki, otwory, gwinty czy krawędzie, które powodują lokalne zwiększenie naprężeń w materiale.
Ostre krawędzie zwiększają lokalne naprężenia (spiętrzenie naprężeń) nawet kilkukrotnie w stosunku do naprężeń nominalnych. To zjawisko znacznie przyspiesza proces zmęczeniowy i może prowadzić do pęknięć.
Stosowanie łagodnych zaokrągleń. Zamiast ostrych przejść między średnicami wału, stosuj promienie zaokrągleń.
Minimalny promień. Zaleca się, aby promień zaokrąglenia był co najmniej 0,1–0,2-krotnością mniejszej średnicy wału. Większy promień zmniejsza koncentrację naprężeń, rozkładając je bardziej równomiernie.
Promienie przejściowe w odsadzeniach ustalających (takich na których tworzą powierzchnię oporową) – R ≥ 0,5h. Dla odsadzeń swobodnych promień najlepiej jeśli możliwie duży.
h- wysokość ścianki osadzonej
Osadzenia piast w celu redukcji naprężeń
![]() |
![]() |
![]() |
Unikanie nagłych zmian średnicy – Stopniowe przejścia. Jeśli zmiana średnicy jest konieczna, projektuj stopniowe przejścia lub stożkowe zwężenia. Tak aby większa średnica była w stosunku ok. 1.2 do mniejszej średnicy. Zaleca się także stosowanie małych kątów (np. 15–30°) w przypadku stożków.
Wysokość odsadzeń czopów h ≤ 0,1d
d- średnica czopa
Odpowiednie dobranie wymiarów
Odsadzenia wałów
Optymalizacja rowków i otworów
Rowki na pierścienie osadcze projektuje się z łagodnymi krawędziami i promieniami. Należy unikać rowków, które mają ostre krawędzie. W przypadku wykonywania otworów w wale, należy zlokalizować je w miejscach o niższym naprężeniu.
Gwinty są w rzeczywistości karbami, które mogą prowadzić do koncentracji naprężeń. Należy unikać nagłego zakończenia gwintu.
Obróbka powierzchniowa w miejscach zaokrągleń zmniejsza ryzyko powstawania mikropęknięć. Takich jak polerowanie lub inne zmniejszenie chropowatości. Dla czopów szlifowanych – stosuje się uskok – 0,3-0,6 mm dla wybiegu tarczy szlifierskiej o łagodnym zaokrągleniu odsadzenia.
zbyt bliskie usadowienie wpustu powoduje spiętrzenie naprężeń między ujściem czopa a karbem na wpuście. Należy unikać.
![]() |
![]() |
Użycie metod obliczeniowych lub cyfrowych modeli obliczeniowych, aby określić wpływ geometrii na koncentrację naprężeń. Analiza metodą elementów skończonych (FEM/MES) pozwoli zlokalizować miejsca koncentracji naprężeń i zoptymalizować kształt w formie cyfrowej, przed fizycznym wykonaniem wału.
Dobrać odpowieni materiał na wały
1.Wytrzymałość mechaniczna
Materiał musi wytrzymywać obciążenia statyczne i dynamiczne (moment skręcający, siły zginające, ugięcia). Wały narażone na wysokie naprężenia powinny być wykonane z materiałów o wysokiej wytrzymałości na rozciąganie.
2.Odporność na zmęczenie
Wały pracujące pod zmiennymi obciążeniami wymagają materiałów o wysokiej trwałej wytrzymałości na obciążenia zmienne.
3.Odporność na korozję
W warunkach agresywnych środowisk (np. morskim, chemicznym) należy stosować materiały odporne na korozję, takie jak stal nierdzewna lub stopy aluminium.
4.Możliwość obróbki cieplnej i mechanicznej
Materiał powinien nadawać się do hartowania, odpuszczania lub innych metod obróbki cieplnej w celu zwiększenia twardości powierzchniowej i wytrzymałości.
Wały o skomplikowanych kształtach, np. wały okrętowe, wymagają materiałów łatwych w obróbce skrawaniem.
5.Koszty
Wybór materiału zależy również od budżetu. Trwałe materiały, takie jak stale stopowe, są droższe, ale oferują dłuższą żywotność wału. Mimo to wybór zawsze powinien być taki, aby spełniać wszystkie wymagania jak najniższym kosztem.